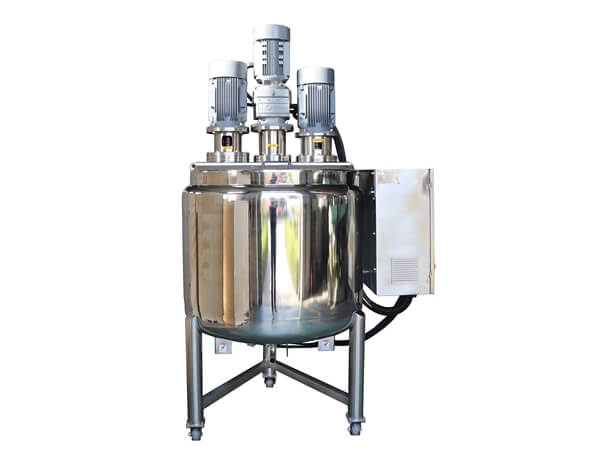
Multishaft Agitated Vessel
Multishaft Agitated Vesse Used throughout nearly every process industry, Multi-Shaft Mixers are robust and versatile. Available in a variety of configurations, as either dual shaft mixers or triple shaft mixers depending on batch characteristics, Multishaft Agitated Vessel Mixers accommodate a flexible range of shear input and viscosities up to several hundred thousand centipoise. The mixer’s basic design consists of two or more independently driven agitators working in tandem to ensure fine solids dispersion, efficient turnover and uniform heating/cooling.
Why Multi-Shaft?
Laminar as well as turbulent mixing zone in the same vessel having viscous media. Overall mixing and homogenization in the same vessel simultaneously even in viscous environment.
Multishaft Agitated Vessel Working Principle
A high speed disperser or homogenizer is used to produce fine dispersion, wetting/dissolving powder producing emulsion etc.
When the viscosity or solid concentration increases the flow ability of material is reduced and heating is observed near HSD / Homogenizer which is not desirable for many applications.
Anchor or Heli-anchor job is to move materials away from high shear zone and provide fresh feed to this zone for processing. Apart from this it also takes care of overall mixing requirement.
Many application requires heat transfer from vessel wall but, due to high viscosity and thickness of materials, scrappers are used.
Apart from the above, scrappers are also used for the applications where the materials have tendency to stick to wall.
In many application where many processes (blending, dispersion, Homogenizations) are to be carried out in the single vessel, combination of impellers are used in the same vessel.
Separate drive for each agitator Mixing and homogenization in viscous media in the same vessel Simultaneous provision for Laminar as well as turbulent mixing zone in the same mixing vessel, Multi-agitator mixer/reactors
Consist of
- Anchor (2,3 or 4 wing)/ Heli-Anchor for overall mixing.
- High Speed Disperser (CAWL DISK / SAWTOOTH) / Homogenizer (Rotor Stator Type)
- Axial flow impeller system
Tip Velocity
- Slow speed = 1 to 3 m/sec
- High Speed = 15 to 40 m/sec
Products typically mixed include:
Window Sealants • Cosmetic Creams • Hot Melt Adhesives • Silicone Rubbers • Pharmaceutical Granulations • Munitions • Construction Caulks • Offset Inks • Lotions • Plastisols • Epoxy Resins • Ceramic Pastes • Polyurethanes • Mascara • Battery Paste • Roofing Sealants • Pyrotechnics • Metal Powders • Medical Patch Adhesives • Carbon Pastes • Printing Inks • Viscous Greases • Health Care Ointments • Grinding Wheel Compounds • Dental Compounds • Explosives • Plastisols • Conductive Inks • Food Coatings • Toothpaste • Solder Pastes • Granulations
Application
Printing inks, Sealants, Caulks, Hot melt adhesives, Magnetic media slurry, emulsions in viscous media, dispersion/homogenization of high and low viscosity fluids Mixing of high viscosity with low viscosity fluids Formulation with high solid content Emulsion in viscous media.
Design Conditions
- Atmospheric
- Pressure or under vacuum
- Jacket/limpet for heat transfer
Sanitary design for food and pharma application
FEATURE
Versatile and cost effective for mixing, dispersion or homogenization in thick or viscous media.
Avoid dead spot or low intensity mixing zone Can be used for Newtonian as well as non-Newtonian fluids.
Anchor/Heli-Anchor can be fitted with scrapper for better heat transfer in viscous media or thick slurry with high solid concentration
Robust and heavy duty design for demanding application.
Automation
VFD for each drive for better process control and result
SEALING OPTIONS
Slow Speed: Stuffing box / Single or double mechanical seal
High Speed : Double Mechanical Seal
INDUSTRY SERVED
- Food and Pharma
- Cream and lotion
- Cosmetics and toiletries
- Toothpaste
- Chemical
- Agrochemical
- Silicon based adhesive and emulsion
- Polymer and Synthetic fibre